A Comprehensive Overview to Carrying Out Foam Control Solutions in Your Operations
Effective foam control is a crucial aspect of operational efficiency that frequently goes ignored. Comprehending the details of foam generation can significantly impact both productivity and product quality. By analyzing crucial variables such as application compatibility and personnel training, organizations can maximize their foam monitoring initiatives.
Recognizing Foam Obstacles
Foam obstacles are a substantial worry throughout different industries, impacting functional performance and item top quality. The development of extreme foam can hinder procedures such as mixing, transportation, and storage space, resulting in enhanced downtime and waste. In industries like food and beverage, pharmaceuticals, and petrochemicals, foam can disrupt assembly line, causing item inconsistencies and contamination threats.
Additionally, foam can obstruct devices capability, causing costly repairs and maintenance. In wastewater treatment, foam can disrupt clarifier procedures, resulting in lower therapy performance and regulative conformity issues.
Understanding the underlying sources of foam generation is critical for efficient monitoring. Aspects such as surfactants, temperature level variations, and agitation degrees can all add to foam production. Determining these components allows markets to apply targeted strategies that lessen foam development while maintaining product stability.
Sorts Of Foam Control Solutions
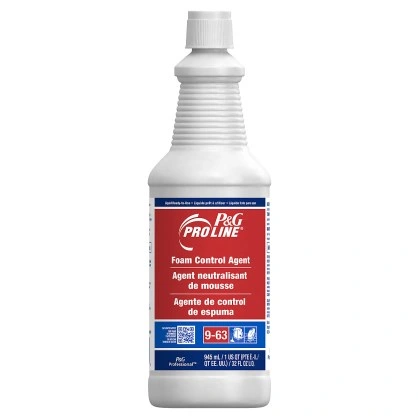
Mechanical remedies entail using gadgets such as foam skimmers or defoamers. These tools physically get rid of foam from the surface area of liquids, therefore stopping overflow and preserving optimum levels in reactors and tanks. Chemical services, on the other hand, consist of the application of defoaming representatives-- materials that disrupt the foam structure, leading to its collapse. These agents can be silicone-based, natural, or aqueous, each offering distinct benefits depending on the application environment.
Last but not least, operational approaches focus on process adjustments. This may involve modifying equipment parameters, such as temperature and pressure, or changing the flow rates of liquids to minimize foam generation. Additionally, applying great housekeeping methods can likewise reduce foam formation by decreasing pollutants that contribute to foam stability.
Choosing the ideal foam control solution includes examining the certain demands of the procedure, consisting of the kind of procedure, the qualities of the materials involved, and safety factors to consider.
Choosing the Right Products
Selecting the ideal foam control products requires an extensive understanding of the details application and its one-of-a-kind challenges. Elements such as the kind of foam, the setting in which it takes place, and the desired outcome all play crucial roles in product option. Foam Control. As an example, in industries like food processing, it is imperative to select food-grade defoamers that comply with safety laws while effectively managing foam.
Furthermore, consider the viscosity of the fluid where the foam issue exists. Some products are formulated for low-viscosity applications, while others are tailored for thicker liquids. Compatibility with existing procedures is another important aspect; the selected foam control representatives ought to incorporate perfectly without interfering with general procedures.
Another important factor is the technique of application. Some items might require dilution, while others you can try this out can be used directly. Analyzing the ease of use and the needed dose can provide insights into the product's performance and cost-effectiveness.
Implementation Techniques
Effective implementation techniques for foam control services need a methodical strategy that straightens item option with functional demands. The initial step involves a thorough evaluation of the procedures where foam occurs, identifying specific areas that necessitate intervention. By engaging cross-functional teams, consisting of manufacturing, design, and top quality assurance, companies can collect understandings that notify the choice of the most efficient foam control products.
Next, it is vital to develop clear goals for foam reduction, making sure that these objectives are quantifiable and possible. This might include specifying acceptable foam degrees and the timelines for implementation. Training workers on the properties and application approaches of chosen foam control representatives is similarly important, as correct usage is essential for ideal results.
Furthermore, incorporating foam control services right into existing process calls for cautious preparation. Ultimately, a well-structured approach will certainly enhance functional performance while efficiently taking care of foam-related challenges.
Tracking and Reviewing Efficiency
Surveillance and evaluating the efficiency of foam control remedies see page is important for guaranteeing that implemented techniques generate the desired outcomes. This procedure includes organized data collection and evaluation to analyze the performance of foam control representatives and techniques. Key performance indications (KPIs) should be established before execution, permitting a clear baseline against which to determine progression.

Reviewing effectiveness also requires routine testimonials of foam control treatments and representative efficiency. This can be completed via tasting and screening, permitting drivers to determine if current options are fulfilling functional requirements. It is crucial to obtain feedback from team members who interact with these systems daily, as their understandings can reveal operational subtleties that measurable data might neglect.
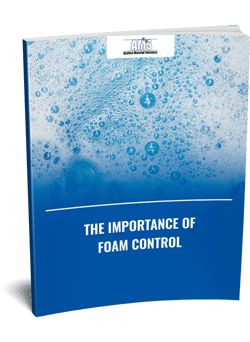
Ultimately, a structured tracking and analysis structure aids recognize essential changes, making certain that foam control solutions continue to be reliable, cost-efficient, and aligned with business objectives.
Verdict
Finally, reliable foam control options are crucial for maximizing functional effectiveness and maintaining item site high quality. A thorough understanding of foam obstacles, integrated with the choice of suitable products and execution methods, helps with the successful monitoring of foam generation. Developing measurable KPIs and spending in personnel educating better improve the effectiveness of foam control actions. Routine monitoring and analysis guarantee continuous renovation, ultimately bring about a much more productive and structured operational setting.
Carrying out good housekeeping methods can additionally reduce foam development by reducing pollutants that add to foam stability.
Selecting the right foam control products calls for a comprehensive understanding of the details application and its distinct obstacles (Foam Control).Effective implementation approaches for foam control solutions call for a systematic technique that straightens product choice with functional needs.In final thought, effective foam control options are important for enhancing functional efficiency and keeping item quality. A complete understanding of foam obstacles, combined with the choice of ideal products and implementation methods, helps with the successful administration of foam generation